Increase Efficiency with Pick-to-Light Systems
Upgrading to a pick-to-light (PTL) system can help save your business both time and money. When your company’s goal is increasing productivity and improving order accuracy, pick-to-light could be the solution. With simple training, PTL provides a cost-effective answer that is easy to implement.
What is Pick-to-Light?
PTL is an order processing system that uses lights or display system to show the operator which items need to be selected, displayed, and the quantity to be called up. It can also be used to reverse the picking process, called Put-to-Light system, so that the goods are received and brought to a place that represents the customer’s order. It uses a lighting device mounted on a floating frame, workstation or mobile trolley to guide the operator to the right place and the right quantity of items needed to fulfil the order.
Imagine a worker being asked to pick a quantity that is prone to picking error, while a PTL operator sees the location and quantity needed to pick. According to bahrns.com, “Voice picking has an expected error rate of 0.2% (two errors per 1,000 picks), which corresponds to an accuracy of 99.8% and 99.98%, respectively.” PTL allows worker to accurately pick quantities of products with improving productivity in warehouse operations.
Pick-to-light is the fastest operator-based picking system available.
Put-to-light displays support the insertion process by picking multiple orders without the logistics of a putwall. Another cost-saving method of PTL installation is to use an illuminated pick position to display the amount in the pickbay where the display is located. PTL’s display serves as a paper-free picking system that supports the operator in production and assembly.
How can PTL Systems help?
PTL systems eliminate the need for a warehouse or distribution center for paper-based orders. Instead, they can be installed as a mobile shopping cart cluster that can pick up multiple orders on a single trip to the warehouse. Instead of a paper order, the system can be downloaded to a computer in the warehouse management system (or host system) and a light module connected to the pickup location.
Picking systems for light picking are one of the best and most commonly used options for picking in logistics and production. Most pick systems have separate inventory and software, making it difficult for improvements and tracking progress. Pick-to-Light connects to inventory to ensure accuracy and provide valuable insights to improve warehouse performance over time.
After identifying the pick-up location, a light unit indicates the case quantity to be picked and a container box of the product is placed. The picker follows the light signal and the quantity is displayed at the pick-up location, minimizing pickers “search time and operator’s instructions for ordering. To confirm the picking task, the operator presses a button on the illuminated display.
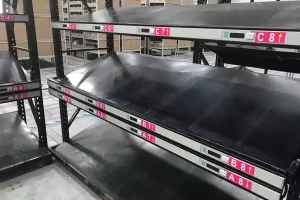
Benefits of Pick-to-Light Systems:
- Paperless & Hands-free
- Wireless
- Improves order accuracy
- Reduces labor costs
- Simple to learn
- Cost-Effective
Technology Behind Pick-to-Light
Voice picking is a relatively new technology, with voice-controlled systems that were used in the 1980s only in industrial applications, while PTL, which has been in use since the 1970s in the US, is considered to be much more mature.
A typical light-based picking system uses different colored LED lights or a series of letters and numbers. The light indicator lights up one after the other to show the picker which order line has been selected. As soon as the picking task is downloaded into the subsystem, a light or light display is installed on a fixed picking station on a shelf (in this case an assembly shelf or warehouse shelf) so that the operator can select any job line at any time.
Items picked in the warehouse are brought into the illuminated system. A light-controlled RF order picker that uses a hardware or software solution (that can be retrofitted to your existing order picker) transmits orders via radio frequency control and LED lights to a computer allowing paperless picking. A controller mounted on the front of the cart guides the picker to the warehouse location and displays the amount of items to be picked and the order of the HF light for each item.
More than 450 pick-up hours, say ten times more pickers, can be achieved in warehouse operations with a paper ordering system. Investment requirements are a key consideration, but picking technology varies too: number of operators (in the case of RF scanning), visual logistics, pick-to-light software, voice-controlled picking, number of pick-up points and, in some cases, PTL picking.
Is PTL right for your business?
What makes Pick-to-Light the most accurate and fastest picking automation system is its good speed and high throughput, however, it requires a higher initial investment in terms of voice and RF and is less productive for high-speed applications.
PTL is the fastest operator-based picking system available, so if increasing productivity is your goal, it’s a great option. As a leading picking operations method, it provides an excellent example of how performance and quality can be improved with light signals and operator guidance can be improved. PTL has a fundamental advantage because its visual technology supports a faster pick rate with amazing accuracy.
Over the past two decades, RF-Light Direct Picking has proved to be one of the key technologies used to increase pick speeds, accuracy and reduce costs. When a company’s aim is increasing productivity, improving order accuracy, simplifying training and reducing labor costs, PTL provides a cost-effective solution that is easy to implement.
In order fulfilment, the picking function is vital to the overall operation, but also can contains a lot of human-error inefficiencies. Fortunately, light picking systems are a great option because they are simple to teach and learn.
0 Comments